- Undergraduate
Bachelor's Degrees
Bachelor of ArtsBachelor of EngineeringDual-Degree ProgramUndergraduate AdmissionsUndergraduate Experience
- Graduate
Graduate Experience
- Research
- Entrepreneurship
- Community
- About
-
Search
All Thayer News
Dartmouth Engineering Receives NASA Grant to Develop Sensor Materials That Can Take the Heat
Oct 03, 2022 | by Catha Mayor
Dartmouth Engineering Professor Yan Li will lead the effort to design new materials for self-powering sensors that can withstand higher temperatures than conventional sensor materials. "For sensing, energy storage, and energy harvesting capability in space, temperature tolerance is important," says Li. "Current materials can only perform at up to 200 degrees Celsius. Above that, all functionality is quickly lost."
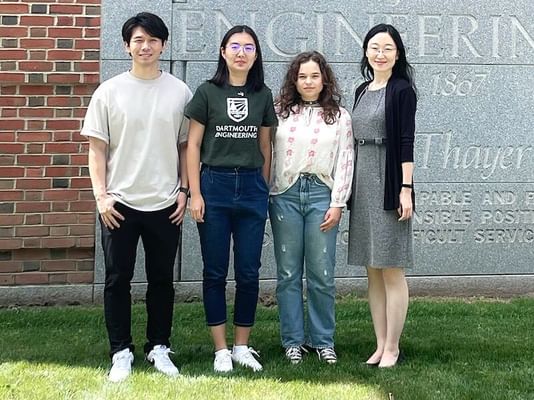
Professor Yan Li and her team: PhD students Huan Zhao and Xiangbei Liu, and Luce Fellow Anisia Tiplea '24.
Li and her team—PhD students Huan Zhao and Xiangbei Liu, and Luce Fellow Anisia Tiplea '24—received $750,000 from NASA's Established Program to Stimulate Competitive Research (EPSCoR). The team aims to develop piezoelectric materials—those that accumulate an electric charge in response to mechanical pressure or movement—for self-powering sensors that can expand NASA's capabilities for damage monitoring and quality control for future in-space manufacturing.
The project, "High-Temperature Effective Piezoelectric Composites for Future Space Self-PoweringSensors," is a collaboration with NASA Jet Propulsion Laboratory (JPL), and also involves Dartmouth's Irving Energy Institute, University of NH, and Sandia National Labs, as well as members of local industry. "These NH companies, including Suprock Technologies and Micro-Precision Technologies, have extensive knowledge in developing high-temperature sensors," says Li, "so they will serve on the advisory board for this project."
The materials being studied are a type called "preceramic polymers" with embedded piezoelectric fillers. While conventional polymers are destroyed by extreme heat, these transform into ceramics.
"At elevated temperatures, preceramic polymers undergo a unique phase transformation into ceramics that exhibit great thermal stability as well as excellent corrosion and creep resistance," says Li, "which is highly desirable for space applications such as 3D printing on the moon or even Mars. The phase transition can also push the temperature limit of existing piezoelectric ceramic-polymer composites."
So why not start with ceramics in the first place? "Ceramics have their own challenges in manufacturing," Li explains. "First of all, they're hard and brittle. The existing machining techniques cannot handle complex geometric features, especially at small scales. Additionally, not all ceramics have piezoelectric effect. Adding piezoelectric particles to the preceramic polymer can introduce sensing and energy harvesting function at higher temperatures while addressing problems such as volume shrinkage and damage formation during the phase transition. Currently, additive manufacturing offers a relatively inexpensive way to fabricate preceramic polymers with complex shapes and hierarchical architectures that are otherwise impossible to achieve through machining.
"The flexibility to control the material structure architecture as well as the phase transition will allow us to try many different things and see—How is the piezoelectric effect? How is the sensing and energy storage capability when different structure architectures are used? We don't know yet. Nobody has done this before."
For contacts and other media information visit our Media Resources page.