- Undergraduate
Bachelor's Degrees
Bachelor of ArtsBachelor of EngineeringDual-Degree ProgramUndergraduate AdmissionsUndergraduate Experience
- Graduate
Graduate Experience
- Research
- Entrepreneurship
- Community
- About
-
Search
All Thayer News
Amping Up the Skies: Designing the future of electric air travel
Sep 13, 2024 | by Theresa D'Orsi | Dartmouth Engineer
As technology leader for aviation electric propulsion, Satish Prabhakaran Th'05 sits at the intersection of aerospace technology and the next generation of products. His latest effort at GE Aerospace Research in Schenectady, NY, involves one of the toughest modern-day engineering challenges: electric air travel. With aviation accounting for about 2.5 percent of global CO2 emissions, hybrid electric propulsion technologies could do a lot to help bring the number down.
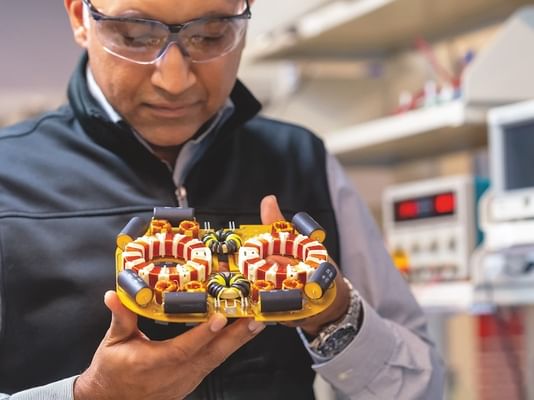
"We're trying to build a mini substation inside an aircraft—so everything we'd do to power a small village—without making it any bigger." —Satish Prabhakaran Th'05
But because of limits on space and weight, this crucial electronic componentry needs to be robust, compact, and light. "We're actually aiming for the size of a suitcase," says the electrical engineer. "We've got to take all the things that happen in the lab, and then we've got to go invent the future of so many other things to make these technologies real." Here, he discusses his flight plan.
You've been managing complex teams for the past decade. What makes a good team member? What makes a good leader?
The work that I've been involved with more recently is all about electric propulsion. We're designing our next engines as we seek decarbonization. The aviation industry has a commitment to get to net zero emissions by 2050. To do that, there's got to be a rather big step change in the kind of technologies we introduce. I sit at the confluence of so many engineering disciplines. We have turbomachinery, we have electrical systems. Thermal management is a big one. And then we've got flight controls software. It's such an exciting space. We want engineers to be right in the middle of all these spaces because none of them can succeed on their own. When I think of a good team member, I think of someone who wants to embrace that diversity, who wants to sit in the middle of a lot of engineering disciplines, most of which they may not feel comfortable with but are willing to learn. There's so much going on. That's the first thing I want to see: the sparkle in people's eyes when they participate in these kinds of programs. I am fortunate to be part of team full of such enthusiasts.
And a good leader is absolutely a team member foremost, someone who works closely with their teams in problem solving We also need leadership beyond the technology itself. New propulsion systems transcend multiple partners beyond research and development. As a leader, one has to champion these technologies with collaborators such as airframers, regulatory agencies, manufacturing partners. And there's a really high bar on safety, which we respect a lot. How does all this technology come together—not only across GE but across industry, across so many organizations like the Federal Aviation Administration or NASA, so many groups that are involved. Leadership in this space requires patience and strategic processes to advance our technology and manufacturing readiness in collaboration with the broader aerospace network.
What are your favorite aspects of your role—working with your team members, tackling the science, taking a broader view across the landscape and plugging in those other systems?
One of the reasons I've stayed at GE so long is because I get to do all of those things. I've been a technologist. I've led a team advancing electrical technologies for potential product insertions. And now, in my current role, I manage the platform of hybrid electric propulsion technologies at GE Aerospace Research. It's a liaison role. I work closely with our business segments on their technology and product roadmaps; I enjoy the strategic outlook. Back at base, we have several labs working on several demonstrations—the sheer number of tests in play is awesome!
How does your PhD research when you were at Thayer inform what you're doing now?
I was with Charlie Sullivan and his group working on miniaturizing components that went into elements that did power conversion for mobile computing platforms. When I came to GE, I was looking at power conversion at about six orders of magnitude higher, such as for wind turbine or a gas turbine. Daunting! But when you take a step back and look at all of these systems, they want to do something similar: perform more at the same size or get smaller with the same performance. Thematically, it's not very different. Many of the same foundational strategies to miniaturize components apply here no matter what scale of power they process. It is industrial R&D with a whole new layer of product transition. The aspects of bringing research to reality has been well worth it.
I gravitated to aerospace because it's very challenging to introduce new ideas into this industry. This is a business with long cycle of development where you need really safe and robust technologies. We're trying to build a mini substation inside an aircraft—so everything we'd do to power a small village or a small community. That's the kind of power we're trying to put on an airplane without making it any bigger. Weight and volume are the primary driving factors for any technology. As we seek to compress our technologies, we conflict the physics of scaling and require new supply chain strategies, new manufacturing processes. It's not just sandbox stuff that gets to fly the next day. There's an impressive number of steps that every technology has to go through before it eventually flies. There is rich opportunity for breaking new ground on so many fronts.
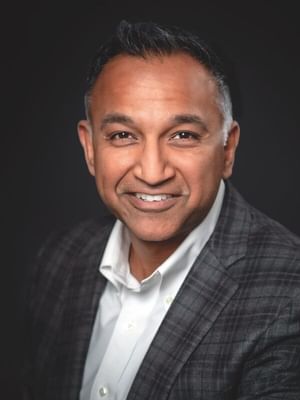
"We're actually inventing a new form of flight. ... This is forcing the research community to become more applied so that we understand the realisms of flight."
Why can't you just scale up or scale down the current technology?
If you have a problem with, say, an electric car, you can pull over. You can't do that on an airplane. Safety is fundamentally at the foundation of everything that we do. We need robust, redundant, and reliable solutions. It's not just about making it small. Building in the resilience to survive long flight cycles, harsh environments through the lifecycle is critical. Today's technologies, when iterated to meet these demands, drop out of the race soon. At GE Aerospace, we go through a rigorous multi-generational technology maturation campaign to prove out new designs. Often state of art isn't going to get you there. We work on new materials that can scale more favorably than present-day solutions. At one end of the spectrum of our developments, we have technologists focused on fundamental aspects of materials and semiconductors, and at the other end, we are building out demonstrations toward flight. The ability to control the sheer breadth of the design space at GE is something I am proud to be part of.
So you're seeing things that don't even exist till tomorrow …
… And we get to walk that journey back and forth. Historically, as a researcher, I might have been more academic, working on the fundamental stuff and throwing it across the fence and hoping somebody would graduate it to a product. But now, let's keep in mind we're actually inventing a new form of flight. Nobody's done this before. This is forcing the research community to become more applied so that we understand the realisms of flight. It's also forcing the product community to become more technologically savvy. We're all coming at it from different directions, and then we might meet and then go back and invent again at the fundamental places we come from. So, my friends in the business can go back and say, we just have no way of manufacturing these things, but we recognize we've got to find a way. They're busy understanding how to manufacture all the fundamental technologies and at the same time we know we can make them better.
Since this is a totally new thing, are you finding that you're having to do some educating among regulatory agencies?
I'd say it's back and forth. There's a lot for us to learn about how these new propulsion systems are certified and made into a safe product. There's a lot of learning to be had. And it's happening—and collaboration is the best way to do it. We're working closely the FAA in progressing technologies with lower emissions and high efficiencies. We participate in several standards committees to help the broader industry implement new standards. Our work is often reviewed by a rich network of government agencies in order for us to disseminate the value of our advancements and get the feedback on the path to certification of these technologies. We have a healthy dialogue that is consistently iterating towards safe implementations.
Do you have a timeline for some of the flight applications or the craft you're working on?
You might have noticed that there's a lot of activity in the small aircraft space, where there's small payloads, short-range aircraft looking at using energy storage such as batteries or fuel cells. I think those types of systems are probably going to be early adopters. For larger payloads and longer ranges, we have more challenges. These larger systems are higher energy and require higher altitudes. The electrification tech maturation is a longer cycle. At GE, we have the RISE engine that aims to achieve 20-percent lower-fuel consumption than current products. In the next decade, we have an exciting lineup of several demonstrators and proof points to advance our developments toward new products.
For contacts and other media information visit our Media Resources page.