
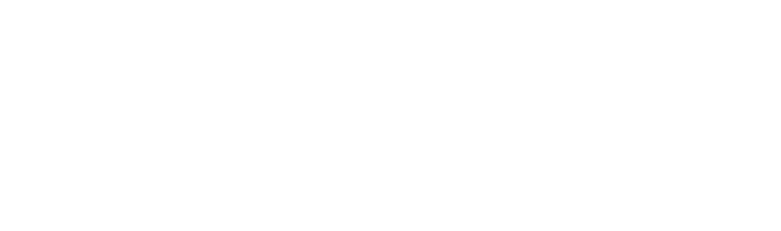
No experience necessary.
Have an idea you’re not sure how to make happen? Need to build something, but don’t know where to start?
We’re here to help!
About the MShop at Dartmouth
The MShop is a unique instructional workshop where problem-solving and teamwork skills are fostered through hands-on learning. We provide our community of scholars with the tools, techniques, and training needed to enable engineering creativity in a safe and collaborative environment.
Our instructors are committed to providing a flexible toolset and a training program accessible to non-experts that builds core competencies in machining and fabrication.
Services
- 3D Printing: Export an STL file from SOLIDWORKS® to be 3D printed.
- SOLIDWORKS® Live: Access and assistance with design, modeling, and analysis.
Equipment
Browse our extensive array of machining and fabrication equipment. Never even used a tool before? We’ll teach you everything you need to know.

Featured Projects

Hours
Monday–Friday
8:00am–4:30pm

Location
Rm 026, Cummings Hall
Building Map | Floor Plan

Contact
+1 (603) 646-9643
mshop@dartmouth.edu
Email mshop@dartmouth.edu for teaching or research requests.
A technical instructor will respond within 1–2 business days.